Plastic extrusion for pipes, sections, and custom shapes
Plastic extrusion for pipes, sections, and custom shapes
Blog Article
A Comprehensive Guide to the Refine and Benefits of Plastic Extrusion
In the huge world of production, plastic extrusion emerges as a important and highly reliable procedure. Transmuting raw plastic right into continual profiles, it provides to a myriad of industries with its impressive adaptability. This overview intends to illuminate the complex actions entailed in this technique, the kinds of plastic proper for extrusion, and the game-changing benefits it brings to the sector. The following discussion promises to unravel the real-world effects of this transformative process.
Recognizing the Fundamentals of Plastic Extrusion
While it might show up facility initially look, the process of plastic extrusion is basically basic - plastic extrusion. It is a high-volume production technique in which raw plastic is thawed and shaped into a continual account. The procedure begins with the feeding of plastic material, in the form of pellets, granules, or powders, right into a warmed barrel. The plastic is after that thawed using a mix of warmth and shear, applied by a turning screw. As soon as the molten plastic reaches the end of the barrel, it is forced with a tiny opening called a die, forming it into a wanted form. The designed plastic is after that cooled down, solidified, and reduced into wanted sizes, finishing the process.
The Technical Process of Plastic Extrusion Explained
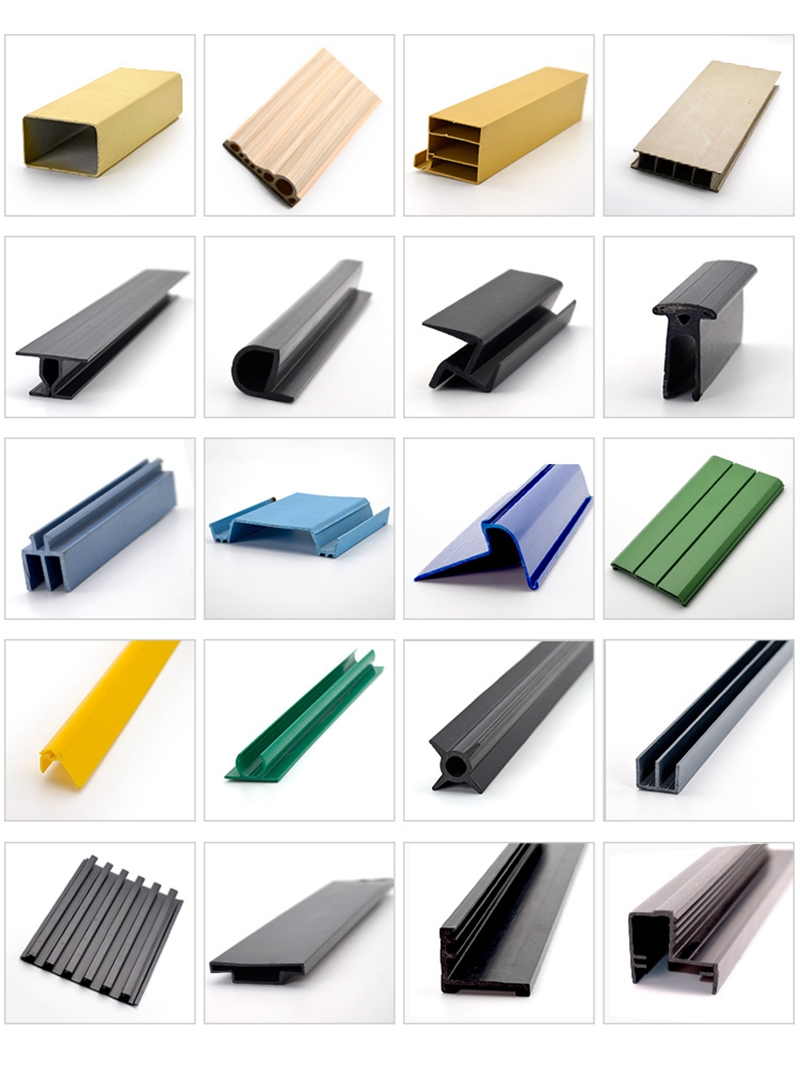
Sorts Of Plastic Suitable for Extrusion
The choice of the appropriate type of plastic is a vital aspect of the extrusion process. Various plastics offer distinct residential properties, making them a lot more matched to specific applications. Recognizing these plastic types can considerably improve the extrusion procedure.
Contrasting Plastic Extrusion to Various Other Plastic Forming Approaches
Comprehending the sorts of plastic ideal for extrusion leads the way for page a broader discussion on just how plastic extrusion compares to various other plastic developing techniques. These consist of injection molding, blow molding, and thermoforming. Each technique has its one-of-a-kind uses and advantages. Shot molding, as an example, is superb for developing detailed components, while blow molding is ideal for hollow things like bottles. Thermoforming excels Home Page at creating shallow or big parts. Plastic extrusion is unrivaled when it comes to developing constant accounts, such as gaskets, seals, and pipes. It likewise enables a regular cross-section along the length of the product. Hence, the choice of method mostly depends on the end-product demands and specifications.
Secret Advantages of Plastic Extrusion in Manufacturing
In the realm of production, plastic extrusion provides lots of significant benefits. One noteworthy advantage is the cost-effectiveness of the process, which makes it a financially attractive manufacturing approach. Furthermore, this technique offers premium product versatility and boosted production speed, thereby raising total production performance.
Cost-Effective Production Technique
Plastic extrusion leaps to the forefront as a cost-efficient production technique in manufacturing. Additionally, plastic extrusion calls for much less energy than standard manufacturing methods, contributing to reduced functional costs. In general, the financial benefits make plastic extrusion an extremely eye-catching choice in the production sector.

Superior Item Adaptability
Past the cost-effectiveness of plastic extrusion, one more substantial benefit in producing lies in its exceptional product versatility. This makes plastic extrusion an ideal remedy for industries that call for customized plastic parts, such as automobile, building and construction, and product packaging. In essence, plastic extrusion's item flexibility fosters advancement while enhancing operational efficiency.
Improved Manufacturing Rate
A considerable advantage of plastic extrusion exists in its improved production rate. Couple of various other production procedures can match the speed of plastic extrusion. Additionally, the capability to preserve consistent high-speed production without giving up item high quality sets plastic have a peek at these guys extrusion apart from other methods.
Real-world Applications and Influences of Plastic Extrusion
In the realm of manufacturing, the strategy of plastic extrusion holds extensive significance. The economic advantage of plastic extrusion, largely its economical and high-volume output, has changed production. The industry is persistently aiming for developments in recyclable and biodegradable products, suggesting a future where the benefits of plastic extrusion can be preserved without compromising environmental sustainability.
Conclusion
In verdict, plastic extrusion is a effective and highly reliable method of transforming resources right into varied items. It supplies various benefits over other plastic forming approaches, including cost-effectiveness, high outcome, minimal waste, and style flexibility. Its effect is profoundly felt in numerous sectors such as building and construction, automobile, and durable goods, making it a crucial procedure in today's manufacturing landscape.
Diving deeper into the technological procedure of plastic extrusion, it starts with the choice of the proper plastic material. As soon as cooled, the plastic is reduced into the called for sizes or wound onto reels if the product is a plastic movie or sheet - plastic extrusion. Contrasting Plastic Extrusion to Various Other Plastic Forming Techniques
Recognizing the types of plastic ideal for extrusion paves the means for a wider discussion on just how plastic extrusion stacks up versus other plastic developing approaches. Couple of various other production procedures can match the speed of plastic extrusion.
Report this page